Lean IT: Everything you need to know about its evolution

Which principles do Lean IT follow?
The principles of Lean IT come from Japan and are the reason for Toyota’s success. By following them, companies will be able to better adapt to the customer, definitively eliminating time and production waste.
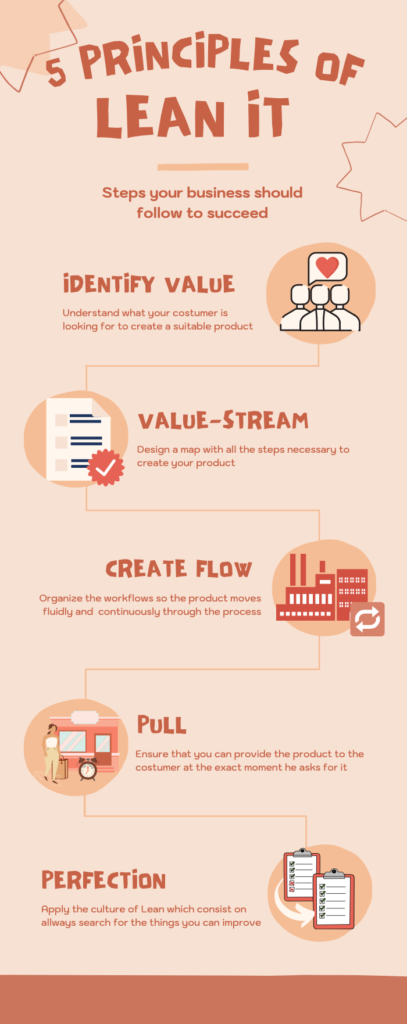
- Identity value: In this case, we understand by value what the consumer is looking for so that the product completely satisfies his needs. This is related to Six Sigma Design since it can help us to identify what the customer is looking for. By understanding the value for our consumers we are managing to eliminate waste and provide a more suitable product.
- Value stream: It consists of designing a map in which you can see each step that a product follows in all departments, from production or design to administration. it is a more visual way to understand the Business operations and eliminate unnecessary steps.
- Flow: Once the unnecessary steps have been eliminated, it is necessary that the product moves through the different processes it has to follow fluidly and continuously, without interruptions or bottlenecks. For this it is necessary to organize the workflows in an adequate way, taking into account good communication between departments. In this way, inventories will be reduced, reducing the cost of storage, and the time dedicated to the production of each product will also be reduced.
- Pull: A production system based on the pull principle takes advantage of improved workflows to provide customers with products as soon as they need them. Unlike the traditional push method, which consists of manufacturing first and then responding to demand, the pull method waits for the customer to demand the product and then obtains the necessary supplies to manufacture it. By having shorter and more efficient workflows, the product will be available in a shorter period than if we used another method and we eliminate the risk of overproduction.
- Perfection: This last step could be the most important. It consists of internalizing the Lean culture and always looking for improvement. All members of the company must understand that they must seek to help the business with small individual actions that together represent a significant improvement. Continuous improvement is key to achieving greater efficiency and productivity at a lower cost.
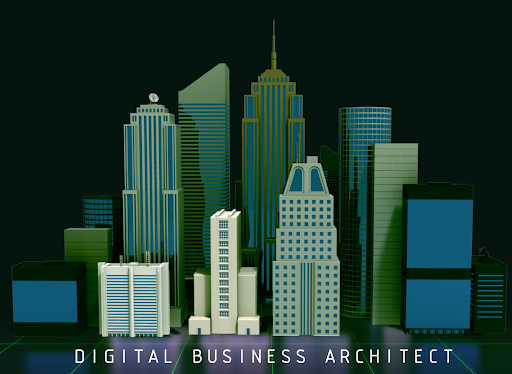
DevOps, Evolution, Kaban, Kaizen, Lean Benefits, Lean It, Lean manufacturing, Lean stages, Manufacturing, Networks, Six Sigma, Techniques, Theory of constraints, TOC, Total quality management, TQM